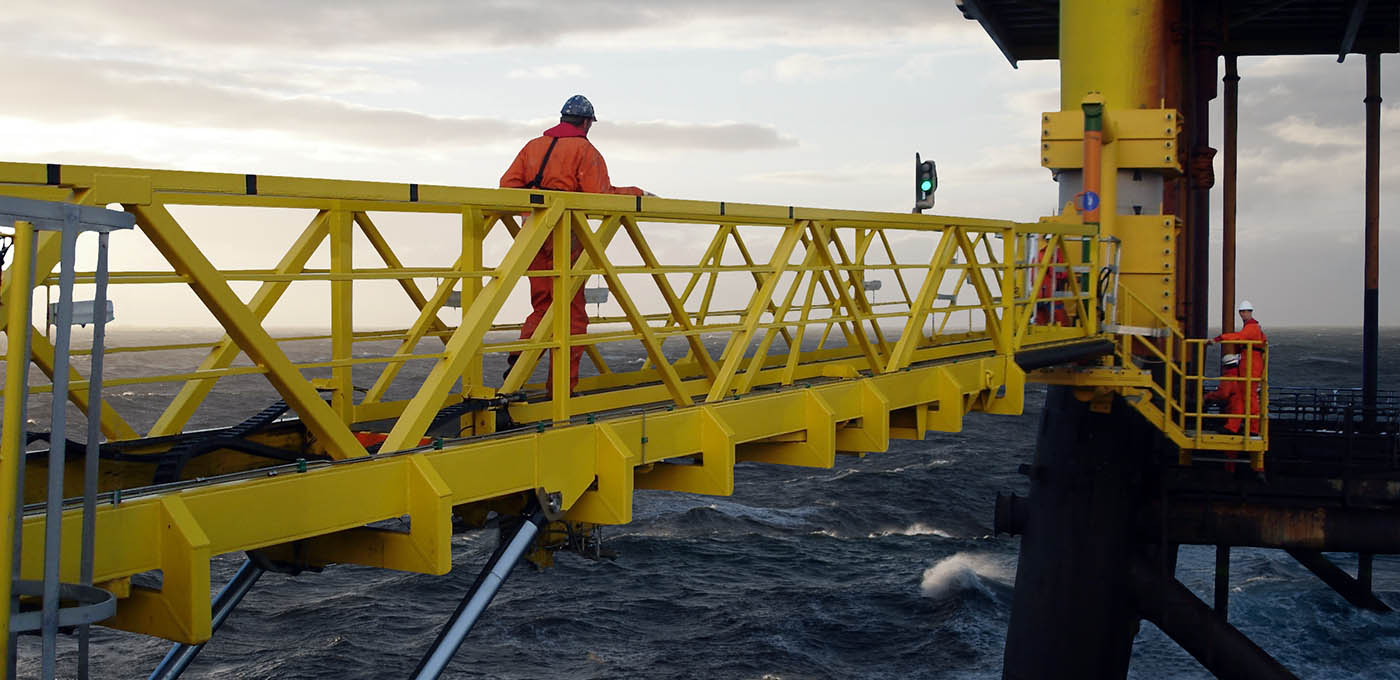
Heave Compensation
Gain motion control and maximize your workability
Overview
Seatools provides turn-key heave compensation solutions for full-motion control over any offshore asset
Seatools has a substantial track record in the field of heave and motion compensation. We have analyzed, designed, and delivered innumerable heave and motion compensation systems: from retrofits applied to existing systems with our standardized HeaveMate® active heave compensation system, to the design and delivery of highly complex full-3D motion compensation equipment. Over the years we have developed an extensive library of algorithms for all types of heave and motion compensation systems, resulting in short project lead times.
- Expertise
-
- Heave compensation for cranes, winches, LARS, gangways, cargo loading systems, draw works, drag heads, and platforms
- Active and passive heave compensation
- Motion compensation (up to 6 degrees of freedom)
- Value creation
-
- Thoroughly tested and fail-safe controllers
- Short lead and commissioning times
- One-stop shop
- Track record
-
- Numerous retrofit and OEM projects
- Full 3D subsea motion control
- Turn-key systems: including mechanical, electric, hydraulic, and software systems
Advanced simulations, standardized control modules, and all required disciplines under one roof – our approach to cost-effective and rapid upgrading projects. Do you want to expand your workability too?
SCOPE
- Feasibility studies, analysis, and troubleshooting
- Custom heave and motion compensation systems
- Upgrades and retrofits
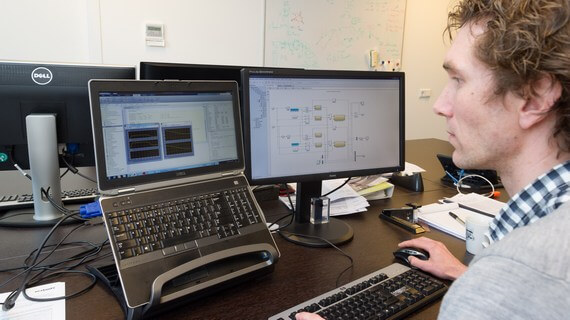
Gain valuable insights for predictable offshore operations
Our advanced simulation capabilities facilitate thorough analysis of any type of (existing) heave and motion compensation system. Extensive simulations may include vessel motions, mechanics, electronics, hydraulics, and controls. Relying on simulations, we analyze a system’s behavior, optimize parameter settings and control strategies, and test system response during mode transitions, extreme circumstances, and failure cases.
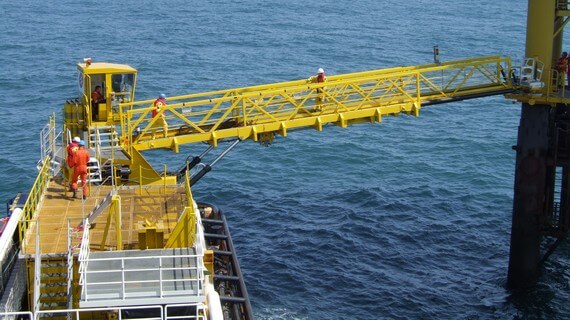
One-stop shop for motion control solutions suiting any of your offshore assets
Custom-made systems include passive heave compensators, active heave compensators, combined passive-active heave compensators, and 3D motion compensators. Seatools can either deliver an OEM package that includes the essentials for heave compensation (i.e. a black box controller with sensors and software), or a fully developed turn-key system that includes mechanical, electric, and hydraulic hardware and software systems. An example of the latter is the OAS heave compensation project. Our scope ranges from system simulations to offshore commissioning and testing.
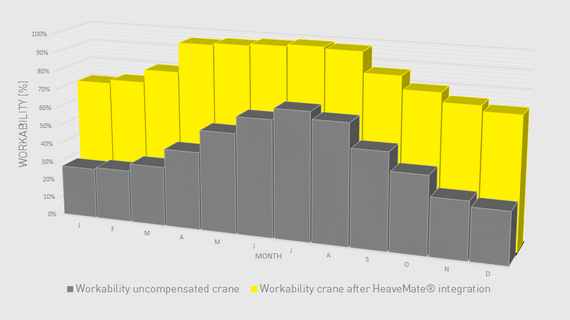
Extend the workability of your existing offshore assets thanks to our standardized solutions
Our HeaveMate® AHC standardized control system facilitates the integration and upgrading of existing systems, such as winches and cranes. We take all the case-specific conditions, requirements, and existing (drive) systems into account, and perform simulations in order to verify the correct performance of the system under any condition. Once all in-depth simulations have been completed, the pre-optimized controller is integrated in the existing system, resulting in a minimum of commissioning time. Seatools is a one-stop shop for upgrades and retrofit projects: our scope includes all required disciplines – including hydraulics and mechanical design – and we deliver our solutions ready-for-use.
HOW WE CREATE VALUE
-
One-stop shop
Because we do not only have a strong control engineering department, but also house the complementary engineering disciplines such as mechanical, hydraulic, software, and electrical engineering, clients can outsource full-fledged projects to a single supplier. This benefits quality and lead times first of all, but also means that projects are performed in a far more cost-effective way and shifts the burden of additional project management away from our clients.
-
Thoroughly tested and fail-safe controllers
Thanks to our simulations we deliver first-time-right solutions and fail-safe control system designs. Before a heave compensation system is installed on site, its control system is extensively simulated. Hence we predict the controller’s response to any condition ahead of installation, and implement the most effective control strategy. In addition, already during the design stage our simulations facilitate analysis of system component failure, such as a failing motion sensor. Like this, we create a system that features sufficient fault tolerance.
-
Short lead and commissioning times
Here too our simulation capabilities make the difference. Simulations provide critical insights during the development stage and help us determine the most optimal control strategy as quickly as possible. Simulations also enable us to pre-program the controller’s most optimal settings ahead of commissioning. In addition, Seatools holds an extensive experience base and control algorithm library. In practice, this means our lead times are short and expensive offshore commissioning time is reduced. This has proven to create significant value for our customers, especially during complex projects such as heave compensated gangways.
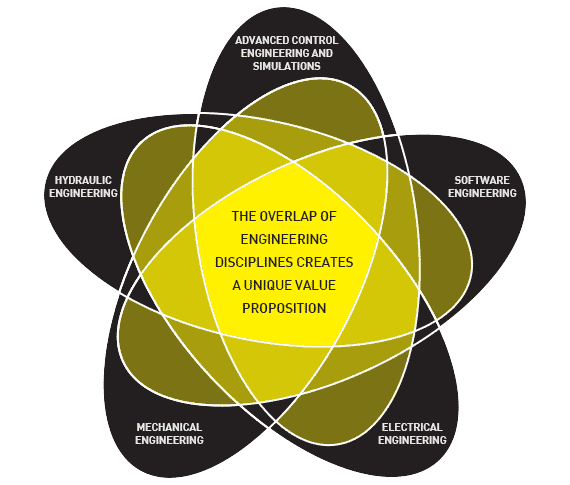
Seatools upgraded a passively compensated LARS system to a combined passively-actively compensated LARS in only 7 weeks. Contact our experts to discuss your project.
Standardized AHC packages
For new and existing equipment
- Winches - Active Heave Compensation Packages
- LARS - Active Heave Compensation Packages
- HeaveMate® - Active Heave Compensation System
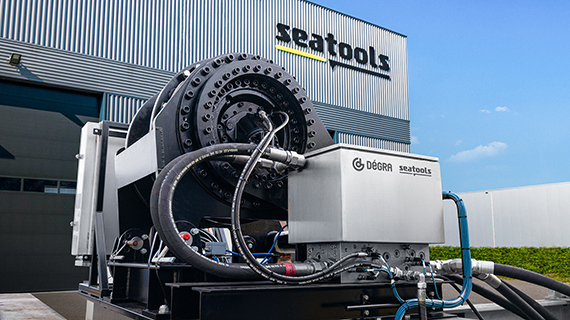
FROM AHC UPGRADES FOR EXISTING AND OEM WINCHES TO FULL-FLEDGED OFFSHORE WINCH SYSTEMS
Seatools distinguishes itself by offering tailor-made active heave-compensated winch solutions for any offshore and subsea application. Our scope ranges from upgrading existing and OEM winches to full-fledged, turn-key offshore winch systems.
Key features:
• Cost-effective solution
• Optimal, fit-for-purpose solutions
• Short lead and commissioning times
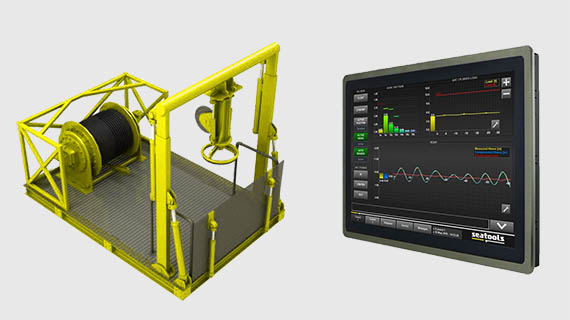
FROM TURN-KEY LARS AHC RETROFIT PROJECTS TO OEM SOLUTIONS FOR subsea hardware MANUFACTURERS
Seatools provides a full range of active heave compensation solutions for both existing and newly built launch and recovery systems (LARS). Our scope of supply can range from turn-key LARS AHC upgrades to LARS OEM AHC solutions.
Key features:
• Cost-effective solution
• One-stop shop
• Short lead and commissioning times
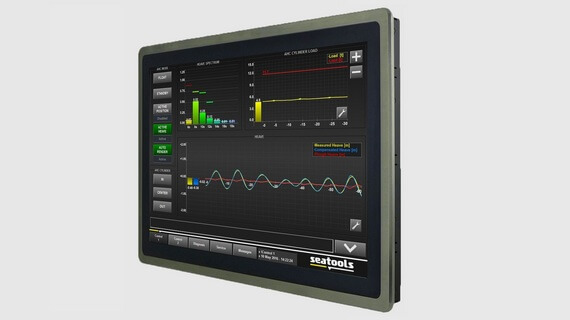
Active heave compensation for offshore assets
The HeaveMate® active heave compensation system is an easy-to-integrate control system for new and existing offshore and subsea hardware equipment, such as winches, cranes, and LARS systems. Seatools offers its standardized HeaveMate® system as a package, including all related services.
Key features:
• Cost-effective solution
• Turn-key delivery
• Short lead and commissioning times thanks to simulations and Auto-tuning
Our simulations ensure proper controller performance under all conditions, and avoid expensive offshore commissioning. Our experts gladly explain what this means for your project.
TRACK RECORD
Our experience is extensive:
from relatively simple 1D AHC retrofits, to complex 3D motion compensator systems
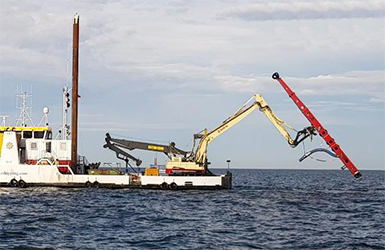
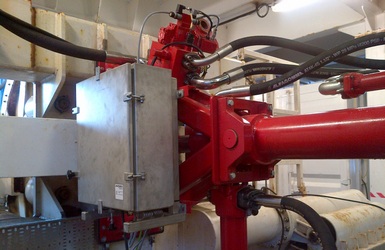
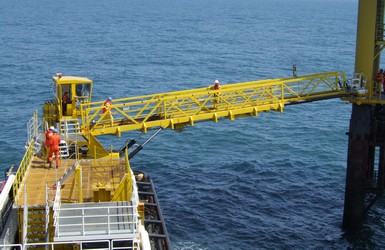
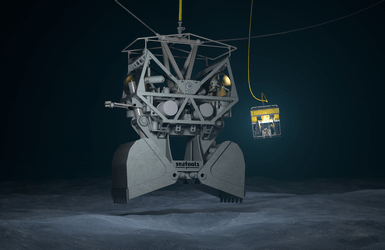
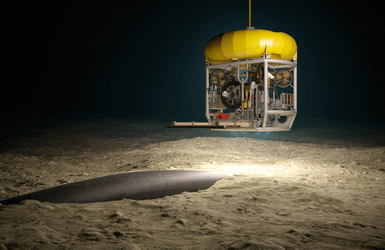
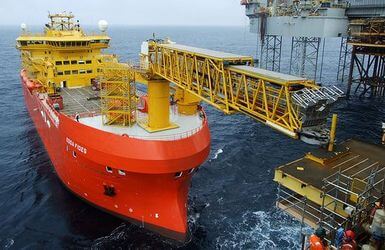
- Project duration:
- 7 weeks
- Client
-
Crane automation for efficient UXO removal operations
For the execution of UXO removal operations, Bodac approached Seatools for the delivery of a crane monitoring and automation solution. By taking the DipMate Pro backhoe dredging monitoring and control system as a basis, the system was further extended with custom developed functionalities such as AHC, tool verticality, and automatic grid survey. With automatic grid survey, the survey tool is automatically positioned by means of controlling slew, boom, stick, and tool arm along a defined pattern. By drawing extensively upon our advanced simulation capabilities, the project was delivered successfully within a short time span which allowed Bodac to perform safe and cost efficient UXO removal operations.
- Date:
- January 2015
- Project duration:
- 7 weeks
- Client:
-
Retrofit AHC LARS – From passively to actively heave-compensated LARS in 7 weeks
On behalf of Deepocean a passively compensated LARS was upgraded to a combined actively and passively heave-compensated LARS system used to deploy a subsea plough.
By means of using our standardized HeaveMate® package in combination with the performance of in-depth simulations for virtual testing and pre-programming of the controller, Seatools was able to comply with the highly challenging delivery time of only 7 weeks, which included commissioning and testing.
- Date:
- March 2005
- Project duration:
- 9 months
- Client:
-
Control system for the first heave-compensated gangway in the industry
In 2005, Offshore Solutions introduced the Offshore Access System (OAS): a heave-compensated gangway that can be mounted on a ship and will facilitate safe transfer of offshore personnel from and to offshore structures.
Seatools delivered the entire control system for the OAS (both hardware and software). A significant part of the system’s design was a detailed simulation of the system, carried out to ensure correct performance of the gangway once deployed.
- Date:
- June 2002
- Project duration:
- 13 months
- Client:
-
Full 3D motion compensation for 70-ton grab at an accuracy range within 20 centimeters
Boskalis and Tideway required a new deep-water dredging method to excavate in challenging soil conditions at a water depth of 150 meters. To this purpose, the Grab Excavation System (GES) was developed.
Seatools designed and built the grab-positioning ROV and its control system, including full-3D motion compensation. We also supplied the control system for the hoisting arrangement, which allowed for a high level of dredging automation and resulted in high production rates.
- Date:
- August 2002
- Project duration:
- 18 months
- Client:
-
Heave compensator for ROV LARS
The ROHP II, developed on behalf of Rijkswaterstaat, is a multipurpose inspection ROV designed for inspection, sampling, survey, and light intervention tasks in waters with strong currents and poor visibility, such as the North Sea.
The complete ROV, including control container and hoist winch, was designed and built by Seatools. In order to keep the vehicle steady and in close proximity to the seabed during inspection and intervention tasks, the system is executed with semi-active heave compensation.
- Date:
- May 2010
- Project duration:
- 12 months
- Client:
-
Full control over a 42-meter gangway in up to 7 meters of heave amplitude
After the success of the first OAS systems, Offshore Solutions approached Seatools with a new challenge: a complete heave compensation system for a far larger (42 meters) offshore gangway, capable of compensating a heave amplitude of 7 meters.
By relying on advanced simulations, Seatools took the same approach as it applied to previous projects. Its choice proved to be a great success once again, resulting in the safe transfer of crews every day.
CONTACT
WOULD YOU LIKE TO DISCUSS YOUR PROJECT WITH OUR EXPERTS?
CONTACT FORM
OTHER CHANNELS
- General
- +31 (0) 186 68 00 00
- info@seatools.com
- Sales
- +31 (0) 186 68 00 00
- sales@seatools.com
- Service (outside office hours, emergency only)
- +31 (0)186 65 00 75