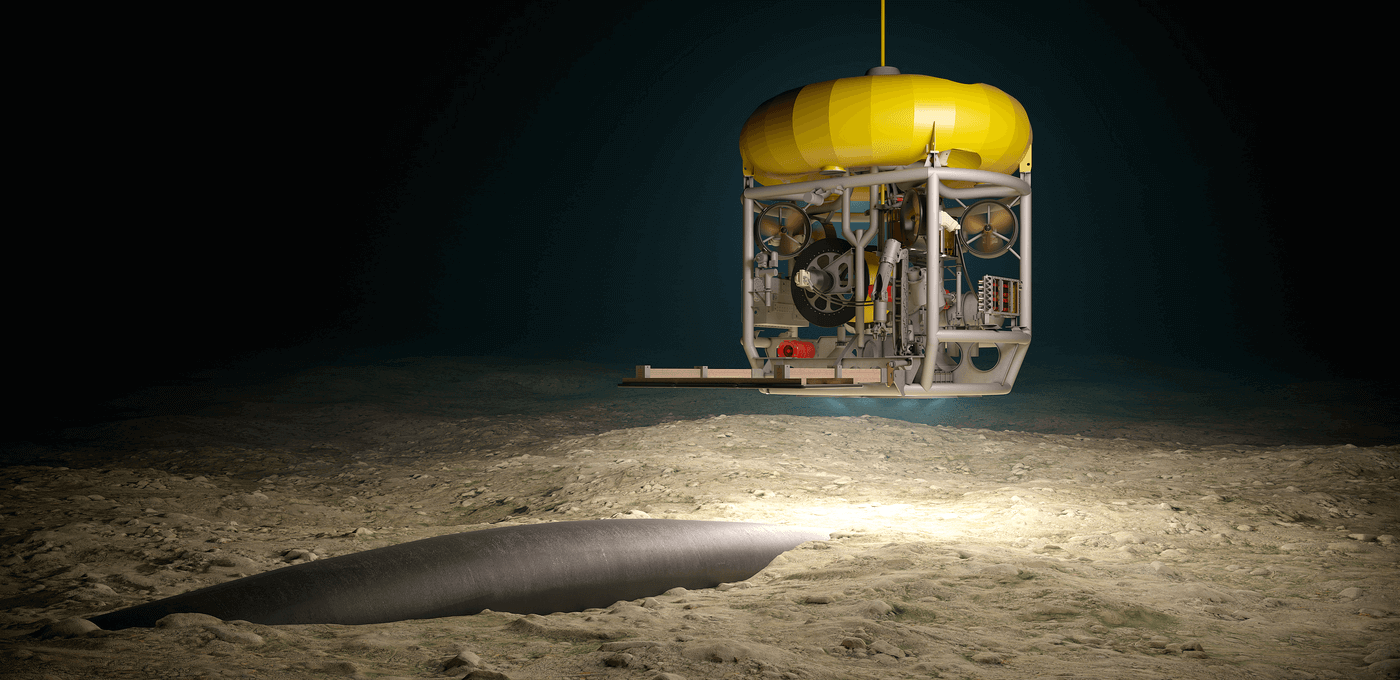
Multi-PurposeInspection ROV - ROHP II
Versatility that drives value creation
Overview
A highly effective multi-purpose inspection ROV
The ROHP II is a multi-purpose inspection ROV designed for inspection, sampling, survey, and light intervention tasks in waters with strong currents and poor visibility, such as the North Sea. Because the ROV should be able to perform a wide variety of tasks, Seatools developed two different modes: the hanging mode and the free-flying mode. As this was never done before, the project posed a significant challenge to our engineers. By exploiting our creative capacities, multiple ingenious solutions were developed and realized, which resulted in a remotely operated vehicle capable of executing all required tasks under a wide range of operational conditions.
- Project scope
-
- Fully fledged inspection ROV, including hoist winch, semi-active heave compensator, and control container.
- Project duration
-
- 18 months
- Client
-
The ROHP-II ROV was designed to perform a wide range of inspection, sampling, surveys, and light intervention tasks. Using a single piece of equipment for multiple tasks drives highly efficient operations. How can we enhance your operations?
Features & Specifications
-
Broad applicability thanks to dual modes
The ROHP II features two modes: the free-flying mode and the hanging mode. In hanging mode, the ROV has relatively large negative buoyancy, and is trailing underneath the mother vessel. This way a large part of the propulsion power can be delivered by the mother vessel, contributing to high survey speeds. In free-flying mode, the ROV is neutrally buoyant, enabling it to move freely in all directions. This allows for inspection of dangerous objects, such as UXO.
-
High survey velocity through combined propulsion
When enabling the hanging mode, the ROHP II trails underneath the mother vessel. As a result, the ROHP’s forward speed is partly delivered by its own propulsion power, and partly by the propulsion power of the mother vessel. Through combined propulsion, the ROHP reaches survey speeds of up to 4 knots, which contributes to, for example, rapid surveys of large areas and ROV pipeline inspection
-
High level of navigation control and automation
Several navigational control features are integrated to assist the operator manoeuvre and navigate the vehicle. These are: auto-heading, auto-altitude, auto-depth, auto-pitch, and a bottom tracking system. Furthermore, the system is executed with semi-active heave compensation to keep the vehicle steady and in close proximity to the seabed during inspection and intervention tasks. The latter is an essential feature when conducting visual inspections in the North Sea’s murky waters.
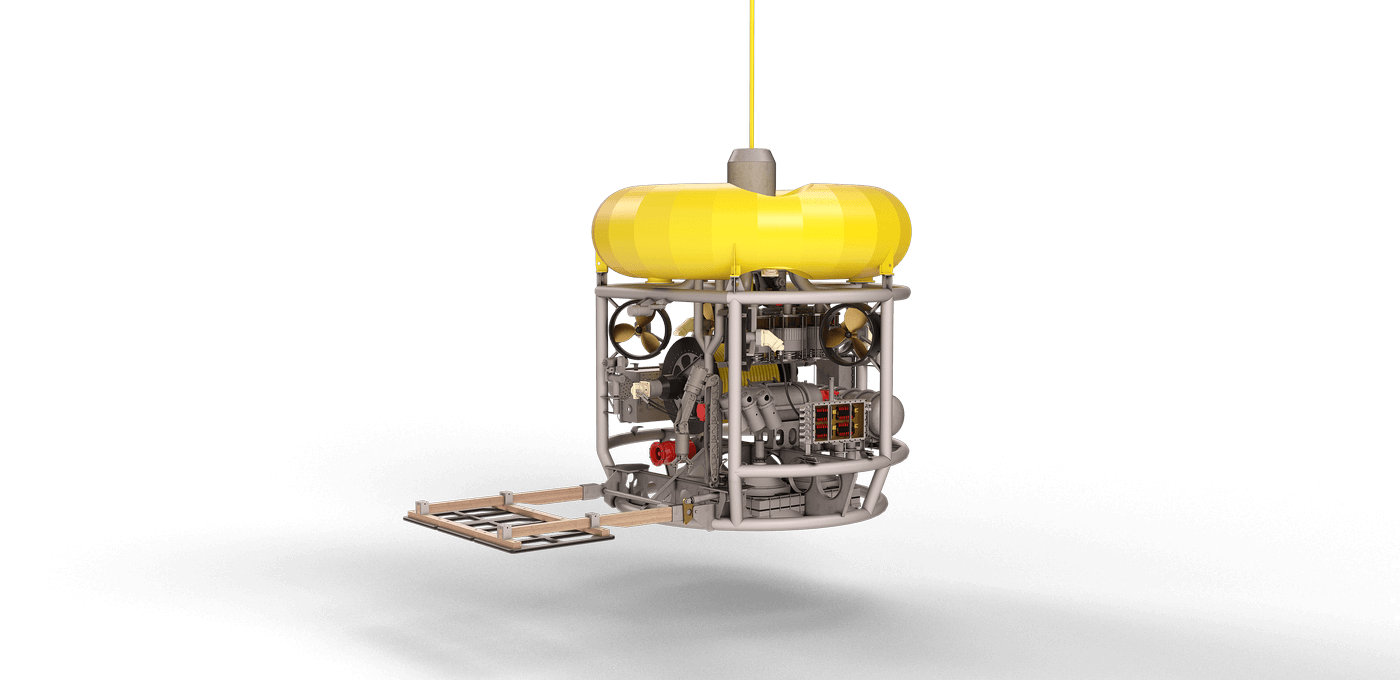
Specifications
- ROV class: (multi-purpose) Inspection ROV
- Purpose of vehicle Inspection, sampling, surveys, and light intervention
- Installed power: 100 kW
- Depth rating: 300 meters
- Payload: 2500 kg (hanging mode)
-
Positioning capabilities:
Auto-depth, Auto-heading, Auto-pitch,
Bottom-tracking
- Manipulator: 7 axis Schilling manipulator (250 kg payload)
- Sampling capabilities: Bottom sampler and water sampler
- Jetting pump capabilities: 40 kW (variable flow and pressure)
- Tether management system: Integrated in ROV (200 m range)
- Vehicle velocity: 4 knots in hanging mode, 2 knots in free-flying mode
Contact
WOULD YOU LIKE TO DISCUSS YOUR PROJECT WITH OUR EXPERTS?
CONTACT FORM
OTHER CHANNELS
- General
- +31 (0) 186 68 00 00
- info@seatools.com
- Sales
- +31 (0) 186 68 00 00
- sales@seatools.com
- Service (outside office hours, emergency only)
- +31 (0)186 65 00 75